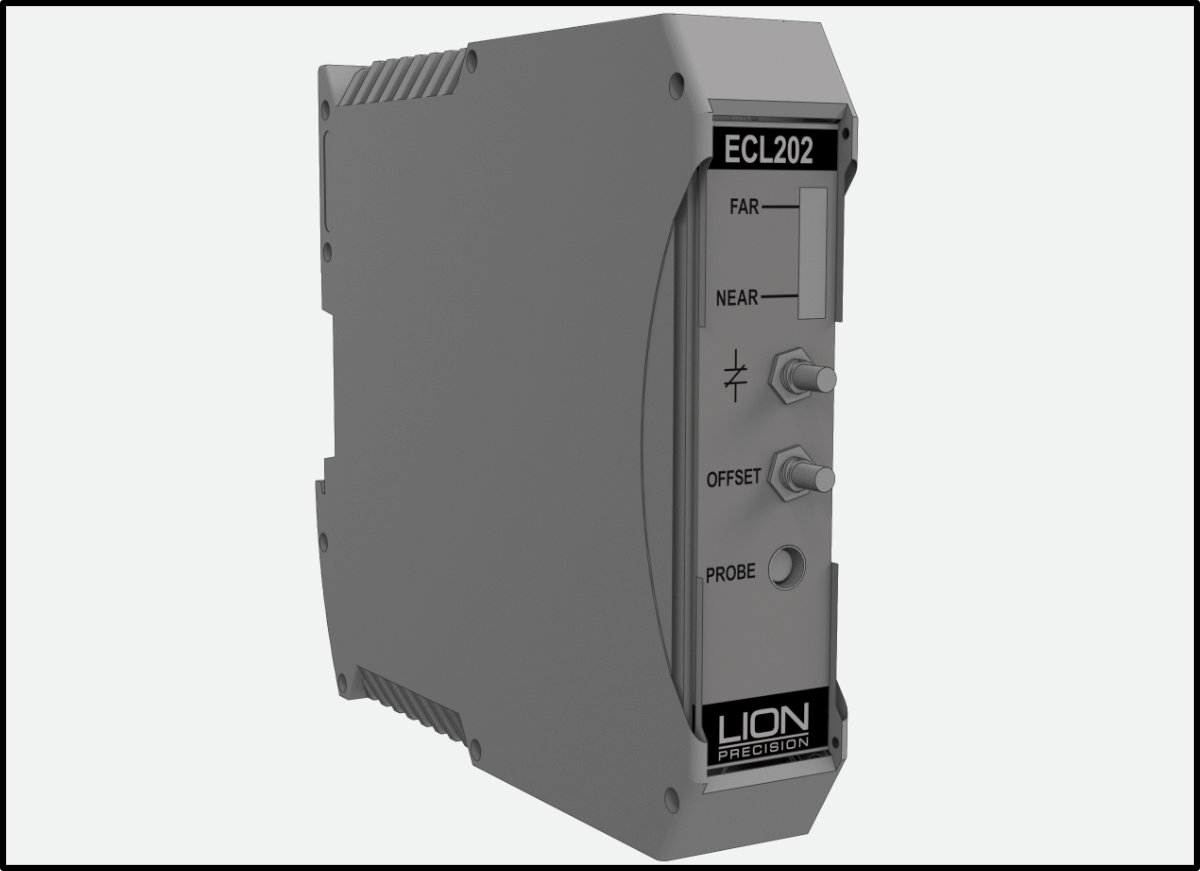
USER’S GUIDE for the
ECL202 / ECL202e – Eddy Current Displacement Sensor
Approvals and Safety Considerations
The ECL202/ECL202e is compliant with the following CE directives:
Safety: 61010-1:2001
EMC: 61326-1, 61326-2-3
To maintain compliance with these standards, the following operating conditions must be maintained:
- All I/O connecting cables must be less than three meters in length
- AC power cables must be rated at a minimum of 250 V and 5 A
- AC power must be connected to a grounded mains outlet rated less than 20 A
- Power supply must have CE certification and provide safety isolation from the mains according to IEC60950 or 61010.
- Sensors must not be attached to parts operating at hazardous voltages in excess of 30 VRMS or 60 VDC
- All external connections must be SELV (Safety Extra Low Voltage).
Use of the equipment in any other manner may impair the safety and EMI protections of the equipment.
ECL202 and ECL202e
The ECL202e is identical to the ECL202 except that the ECL202e resolution is never better than 0.2 µm. For this reason, the ECL202e does not require an export license.
This manual will only refer to the ECL202, but all instructions apply to the ECL202e except where noted.
Description
The Lion Precision ECL202 Eddy-Current Displacement Sensor provides high resolution, noncontact measurement of position changes of a conductive target. The system consists of driver electronics and a probe calibrated for a specific material and range. The calibration information is detailed on a calibration certificate which is shipped with the system.
The ECL202 provides a linear analog voltage proportional to changes in the target position and a digital switched (setpoint) output with a user programmed switching setpoint.
Quick Start Instructions
- Connect the probe to the ECL202.
- The ECL202 is calibrated to a specific probe identified by serial number. The probe serial number must match the “USE PROBE S/N” label on the front of the ECL202.
- Connect the output to a monitoring device.
- Connect then apply power.
- Adjust the probe position so the Range Indicator shows green
Front Panel Controls and Indicators
LED Range Indicator
The Range Indicator monitors and displays the probe position within its calibrated range. The graphic below shows the indicator condition at various points within the calibrated range.
The LED Range Indicator is independent of the output voltage and not affected by the Offset button. Shifting the output voltage by using the Offset button may allow an apparently valid output voltage to exist while the probe is out of range. When the Near or Far LED is red, the probe is out of range and the output voltage is not a reliable indication of the target position.
Offset Button
Pushing the Offset button shifts the DC level of the output voltage to the center of the voltage range (i.e. 5 V for a 0-10 V output). The button will only function when the probe is in the center 20% of its calibrated range (center green LED). If the center green LED on the Range Indicator is not on, the Offset button will not function.
This function establishes a repeatable master point for reference measurements.
- Place good part in the measurement area
- Position probe to center 20% of range (center indicator LED)
- Press Offset button
- All subsequent measurements indicate deviation from center of range (5 V)
Resetting Offset
Hold the Offset button for four seconds to remove any output DC shift.
Setpoint Button
The ECL202 provides an adjustable setpoint at which a switched output activates. The output switch closes when the output voltage is more positive (larger gap) than the user-adjusted setpoint. Pressing the Setpoint button will set the threshold voltage to the current output voltage. The setpoint includes a 0.085V hysteresis, requiring that the sensor output drop 0.085V below the setpoint voltage before the switched output opens.
Analog and Output Signal
The output signal is an analog voltage of 0-10 VDC. The output voltage is proportional to the probe-target gap. As the probe-target gap increases, the voltage becomes more positive. See the included calibration certificate for specific information.
Interpreting the Output Voltage
Output voltage change for a given change in the probe-target gap is called sensitivity. The sensitivity is listed on the calibration certificate.
Change in gap calculation:
Gap Change = Voltage Change / Sensitivity
For example: With a sensitivity of 1V/2 µm and a voltage change of +3 V, the probe-target gap has increased by 6 µm.
Remote Offset and Setpoint
The front panel Offset and Setpoint buttons can be activated remotely. Each remote input connects to an optoisolator. The functions are activated by applying 15-24 V to the remote control input terminals.
Note: Because the remote operation mimics front panel operation, activating the Offset function for more than four seconds will restore factory default value for Offset.
Setpoint Switch Output
When the output voltage is more positive than the user adjusted setpoint voltage, the output switch contacts will close. These contacts have a maximum resistance of 2.5 Ω and can conduct up to 250 mA. The maximum voltage that can be switched is 30VAC/60VDC. The output is a solid state switch closure and can conduct AC or DC.
Bandwidth Selection (ECL202 Only)
A jumper wire on the bandwidth connector selects sensor bandwidth. To select a bandwidth, connect the desired bandwidth terminal to the Bandwidth Select contact. With no jumper, the bandwidth is 15 kHz. Bandwidth specifications are -10%/+30%.
Maximizing Performance
Extension Cables
Sensors which are calibrated with a probe extension cable must be operated with the extension cable to meet specifications. Operating without the extension cable will result in inaccurate measurements.
Probe Mounting
If multiple probes are mounted together, they must be separated by at least three probe diameters.
The area within 3 probe diameters to the sides and 1.5 diameters behind should be kept clear of any metallic objects other than the object to be measured. Otherwise, custom calibration will be required.
Ungrounded Targets
Ungrounded targets have the potential to inject noise into the sensor. If the output is unusually noisy, be sure the target is grounded. On moving/rotating targets this can be accomplished with a small metal brush or thin piece of metal which is connected to ground.
Multiple Sensors
When multiple sensors are used with the same target, the sensors must be synchronized. An interconnecting circuit board connects to the rear of multiple drivers to provide synchronization signals. Multiple sensor orders are shipped with the interconnect board in place and the drivers are pinned together as one unit.
It is critical that each ECL202 be connected to the probe indicated on the “USE PROBE S/N” label on the front of each ECL202.
Connecting to the ECL202
Connection | Description | Notes |
Top-Rear Connector: Remove Offset | ||
No Connection | ||
No Connection | ||
Remote Offset + | + Optoisolator input for Remote Offset function | 15-24 VDC Activates the function |
Remote Offset – | – Optoisolator input for Remote Offset function | |
Top-Front Connector: Remote Setpoint and Switch Output | ||
Remote Threshold – | – Optoisolator input for Setpoint function | 15-24 VDC Activates the function |
Remote Threshold + | + Optoisolator input for Setpoint function | |
Switch | Contact 1 of switched output |
Open: 30 VAC/60 VDC max Closed: 250 mA max |
Switch | Contact 2 of switched output | |
Bottom-Front Connector: Power and Analog Output | ||
Power In | Input Power |
|
Power Ground | Power Ground |
Internally connected together |
Output Signal Ground | Reference for output signal voltage |
|
Output Signal | Output signal voltage |
0-10 VDC |
Bottom-Rear Connector: Bandwidth (ECL202 Only) | ||
Bandwidth Selected | Common point for bandwidth selection jumper |
|
100Hz, 1kHz, 10kHz | Bandwidth selection, connected to Bandwidth Selected |
None = 15 kHz |
Specifications
Parameter |
Specification | Notes | |
Power Requirement | 15-24 VDC, 2.5 W | ||
Resolution @ 15kHz (Typical)1,2 | nonferrous | 0.006 to 0.008%F.S. (ECL202) 0.3 µm or higher (ECL202e) | See calibration sheet for specifics |
ferrous | 0.007 to 0.1%F.S. (ECL202) 0.3 µm or higher (ECL202e) | ||
Linearity1 | ±0.2%F.S. | ||
Error Band1 | ±0.4%F.S. | ||
Analog Output1 | 0-10 VDC, 0 Ω, 15 mA max | ||
Analog Output Update Rate | 15 µS | ||
Setpoint Switch Output | Solid state switch closure: On state: 2.5 Ω, 250 mA max Off state: 30 VAC/60 VDC max | ||
Remote Setpoint and Offset Inputs | 15-24 VDC to activate, 3-7 mA | Optoisolator inputs | |
Driver Operating Environment | 4°C-50°C, IP40 | ||
Probe Operating Environment | Standard Probes | -25°C to +125°C, IP67 | |
High Temp. Probes | -25°C to +200°C, IP63 |
1Actual values depend on probe and range and are listed on the calibration certificate shipped with the product. Contact Lion Precision for replacement certificates.
2In High EMI environments (10 V/m), output noise levels may rise to 30 mV causing resolution to be reduced to 0.3%.
Parameter | Specification | Notes | ||
Temperature Coefficient (Driver | nonferrous | U3 Probe | ±0.04% F.S./°C | Over 15°C to 50°C temperature range |
U5 Probe | ±0.1% F.S./°C | |||
U8 Probe | ±0.04% F.S./°C | |||
U12 Probe | ||||
U18 Probe | ||||
U25 Probe | ||||
U38 Probe | ||||
U50 Probe | ||||
ferrous | U3 Probe | ±0.08% F.S./°C | ||
U5 Probe | ±0.1% F.S./°C | |||
U8 Probe | ±0.04% F.S./°C | |||
U12 Probe | ||||
U18 Probe | ||||
U25 Probe | ||||
U38 Probe | ||||
U50 Probe | ||||
Temperature Coefficient (Probe) | nonferrous | U3 Probe | ±0.04% F.S./°C | Over 15°C to 65°C temperature range |
U5 Probe | ±0.04% F.S./°C | |||
U8 Probe | ±0.02% F.S./°C | |||
U12 Probe | ±0.02% F.S./°C | |||
U18 Probe | ±0.01% F.S./°C | |||
U25 Probe | ||||
U38 Probe | ||||
U50 Probe | ||||
ferrous | U3 Probe | ±0.04% F.S./°C (15°C to 35°C) ±0.08% F.S./°C |
||
U5 Probe | ±0.01% F.S./°C | |||
U8 Probe | ±0.04% F.S./°C | |||
U12 Probe | ±0.03% F.S./°C | |||
U18 Probe | ±0.01% F.S./°C | |||
U25 Probe | ±0.01% F.S./°C | |||
U38 Probe | ±0.02% F.S./°C | |||
U50 Probe | ±0.01% F.S./°C |
Mechanical Detail